半導体への無電解UBMめっき
半導体ウエハー用無電解UBM金めっき加工
近年、半導体ウエハ上実装パッド電極への無電解めっきによるUBM形成(Under Bump Metal)が注目される中、当社は長年培ってきました、プリント配線板等で使用されます実装用金めっき技術を活かし、安定したワイヤーボンディング対応用無電解金めっき加工が可能です。
SRやポリイミドが混在したウエハーにおいても、パッド部へ選択的なボンディング用金めっき加工が可能です。
弊社対応可能プロセス
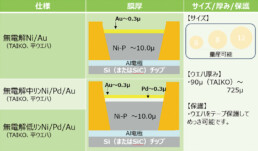
セミオートライン(〜8inch)
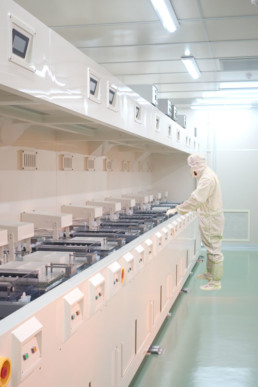
オートライン(〜8inch 試作対応は12inchも可)
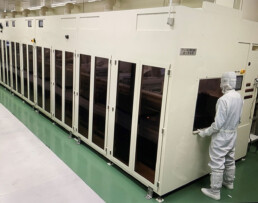
機能めっきのその他のコンテンツ
電子基板への貴金属めっき
基板タイプ | プリント基板 ビルドアップ基板 フレシキブル基板 |
LTCC セラミック基板 |
TAB/COF テープ基板 |
備考 | ||
加工装置 | ラック 全自動 |
ラック 全自動/半自動 |
フープ 全自動 |
|||
加工サイズ (mm) |
510×600 | 200×200 | 材料厚/ 0.025~0.125 材料巾/ 35~165 |
めっき仕様により条件変更有 | ||
電 解 |
Ni(厚み:µm) | 光沢 | (3~5) |
|||
半光沢 | (3~5) |
|||||
無光沢 | (3~5) |
(2~5) |
(0.1~10)※1 |
※1 スルファミン酸系を使用しています。 | ||
Au(厚み:µm) | 純金 | (0.5) |
(0.1~) |
(~1) |
ワイアーボンディング用 Au/Au接合 |
|
硬質 | (0.03~1.0) |
接点用 | ||||
無 電 解 |
Ni(厚み:µm) | Ni-P | (2~5) |
(2~5) |
中Pタイプ | |
Au(厚み:µm) | 薄付 | (0.03~0.05) |
(0.03~0.05) |
表面実装用 半田付け用 |
||
厚付 | (0.1~0.5) |
(0.1~0.8) |
ワイアーボンディング用 Au/Au接合 |
|||
パラジウム(厚み:µm) | 無電解 | (0.1~) |
(0.1~) |
金めっきと組み合わせ使用 | ||
各仕様組合わせでのコンビめっき、部分めっき加工承ります。 | 厚膜印刷基板(Ag系配線)専用工程です。 Cu、W等承ります。 |
無電解Snめっき、レジスト印刷加工も承ります。 |
電解タイプ
めっき仕様 | 対応めっき厚(μm) | 生産能力 | ワークサイズ(mm) |
無光沢Ni/純Au | Ni 0.50〜10.0 | 15,000枚/日 | 一般仕様 100 × 100 〜510 × 600 (MAX 1,000 × 1,000) |
Au 0.03〜1.0 | |||
半光沢Ni/純Au | Ni 0.50〜10.0 | ||
Au 0.03〜1.0 | |||
無光沢Ni/硬質Au | Ni 0.50〜10.0 | 3,000枚/日 | |
Au 0.03〜1.0 | |||
半光沢Ni/硬質Au | Ni 0.50〜10.0 | ||
Au 0.03〜1.0 | |||
半光沢Ni/光沢Ag | Ni 0.50〜10.0 | 2,000枚/日 | |
Ag 0.50〜3.0 | |||
無光沢Niのみ | Ni 0.50〜10.0 | 1,000枚/日 | |
半光沢Niのみ | Ni 0.50〜10.0 | ||
ダイレクト 純Au | Au 0.03〜1.0 | ||
ダイレクト 硬質Au | Au 0.03〜1.0 | ||
ダイレクト 光沢Ag | Ag 0.50〜3.0 | ||
部分Au/光沢Ag ※1 | 各仕様による | 各仕様による | |
2色めっき ※2 | 〃 | 〃 |
電解めっきは、弊社専用の給電接点が必要になります。事前にお打合せを御願い致します。
上記対応めっき厚以外にも、ご相談頂ければ処理は可能です。
※1 部分めっきは、マスク治具・テープマスクによるめっきの他、リード接続部のみの厚付も可
※2 用途に合わせた組み合わせで、片面ずつ別の仕様でめっきが可能
例)
その他の仕様についても、お問合せ下さい。
無電解タイプ
めっき仕様 | めっき種類 | 対応めっき厚(μm) | 生産能力 | ワークサイズ(mm) |
Ni/薄付けAu | Ni | 2〜10 | 5,000枚/日 | 100 × 100〜 610 × 710 |
置換Au | 0.02〜0.08 | |||
Ni/薄付けAu (低腐食型置換Au) | Ni | 2〜10 | ||
低腐食型置換Au | 0.02〜0.08 | |||
部分Ni/薄付けAu (DF対応) | Ni | 2〜10 | 1,000枚/日 | 100 × 100〜 610 × 710 |
低腐食型置換Au | 0.02〜0.08 | |||
Ni/Pd/Au (置換Au) 3層仕様 | Ni | 2〜10 | 5,000枚/日 | 100 × 100〜 570 × 870 |
Pd | 0.02〜1.0 | |||
置換Au | 0.02〜0.04 | |||
Ni/Pd/Au (置換厚付けAu) 3層仕様 | Ni | 2〜10 | ||
Pd | 0.02〜1.0 | |||
置換厚付けAu | 0.05〜0.3 | |||
Ni/Pd/Au (置換Au + 還元Au) 4層仕様 | Ni | 2〜10 | 2,000枚/日 | 100 × 100〜 570 × 870 |
Pd | 0.02〜1.0 | |||
置換Au + 還元Au | 0.05〜0.5 | |||
Ni/厚付けAu (還元Au) | Ni | 2〜10 | 5,000枚/日 | 100 × 100〜570 × 870 |
還元Au | 0.05〜1.0 | |||
ダイレクトAu | 置換Au | 0.02〜0.15 | 1,000枚/日 | 100 × 100〜 610 × 710 |
プリント基板/ビルドアップ基板/フレキシル基板用金めっき加工
無電解NiめっきP濃度 VS ターン数
電解 VS 無電解Auめっき(Ni:5µm、Au:0.5µm)
LTCC基板(セラミック基板)用金めっき加工
LTCC基板のAg系配線への無電解金めっき加工(下地Niめっき)承ります。
耐熱仕様にて、Ni/Pd/Au3層めっきも可能です。
Wafer検査装置
膜厚測定:高精度蛍光X線膜厚計
測定装置:日立ハイテクサイエンス製 FT150
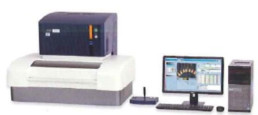
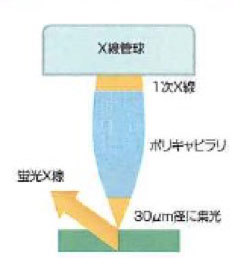
- 薄膜の膜厚測定を高速で簡便に行える最新機種を導入
- ビーム径を30μm まで絞ることができ、100μm を下回る微小Pad の膜厚測定が可能
- 多層膜の測定スピードは従来機種と比較して2倍以上に高速化
外観検査:金属顕微鏡
測定装置:ニコンインステック製 ECLIPSE L300N
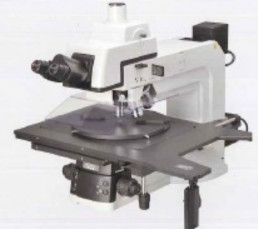
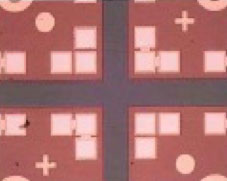
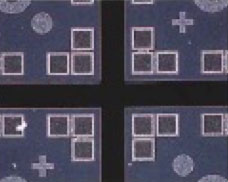
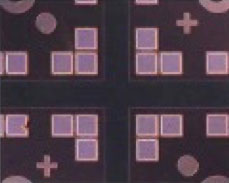
- ウェハー専用ステージを備えた、外観検査装置として実績の高い機種を導入
- 明視野、暗視野、微分干渉など各種観察方法に対応
外観検査:ウェハローダー
測定装置:ニコンインステック製 NWL200TMB86(6,8inch 対応)
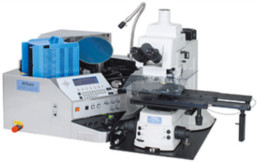
- ウェハの外観のマクロ検査や裏面検査を行い、ウェハを自動で顕微鏡ステージに搬送する装置を導入
- ノッチやオリフラの方向合わせも可能
治工具類の活用
ウェハ移載機
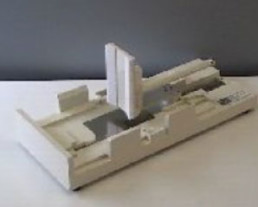
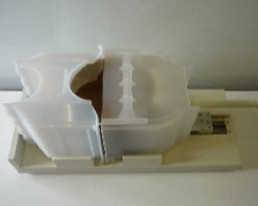
ノッチアライナー
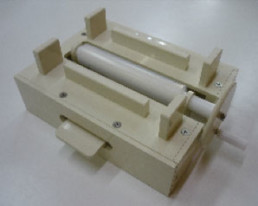
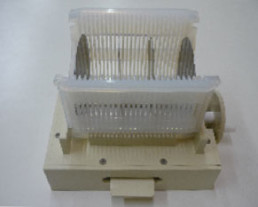
ウェハのハンドリングを少なくし、破損等のリスクを低減するため各種治工具類を導入
機能めっきのその他のコンテンツ
液分析
大和電機諏訪事業所所有装置
イオンクロマトグラフィー | DIONEX製 ICS-1500 |
液体クロマトグラフィー | 島津製作所製 LC-2010A HT |
分光光度計 | 日立ハイテクサイエンス製 U-2910 |
キャピラリー電気泳動 | Agilent製 7100 |
ICP発光分光分析装置 | 日立ハイテクサイエンス製 PS3520-DD |
自動滴定装置 | 東亜DKK製 AUT501、AUT701 |
pHメーター | 東亜DKK製 HM-30R |
表面張力計 | 協和界面科学製 CBVP-A3 |
液中パーティクルカウンター | Sysmex製 APSS-200 |
電気化学測定装置 | 北斗電工製 HZ5000 |
イオンクロマトグラフ
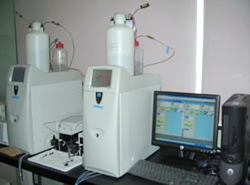

電導度で測定したピークまたは、
UV検出器で 得られたピークから定性定量分析を行う。
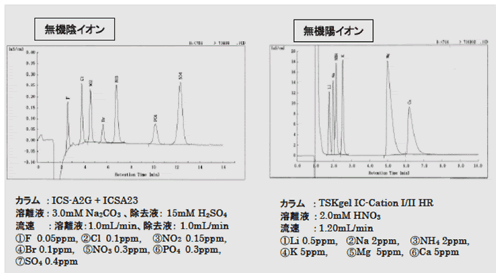
液体クロマトグラフ
液中の添加剤、成分分析など 測定装置:島津製作所製 LC-2010A HT
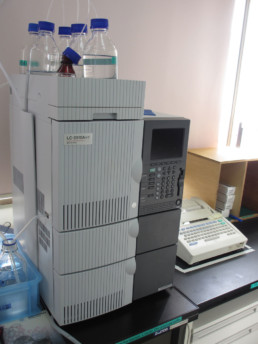
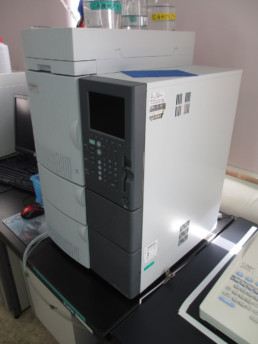
移動相に液体を用いるクロマトグラフィー
熱に弱く、気化しにくいサンプルの分析が可能で、ピーク分離や検出感度に優れる
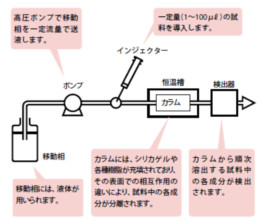
キャピラリー電気泳動
溶液中の有機酸、イオンの定性定量分析
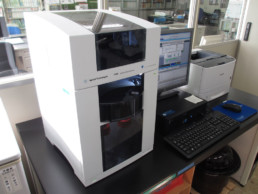
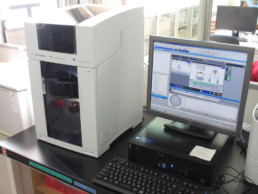
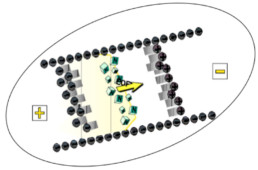
ICP発光分光分析装置

金属塩濃度、金属不純物濃度、Rohs規制物質の分析など測定装置:日立ハイテクサイエンス製 SPS3520DD
サンプル(液体)を蒸発気化、発光させ、分光することにより原子スペクトルを取得
分光された光の波長や強度から元素の種類、量を分析する。
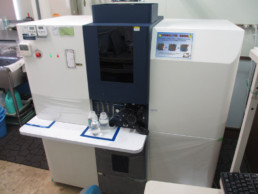
分析精度
分解能:0.004~0.007nm
定量値:数ppb~数十ppb
電気化学測定機
高性能ポテンショスタット/ガルバノスタットにファンクションジェネレータとクーロンメータを内蔵した、オールインワンタイプの電気化学計測ステーションです。
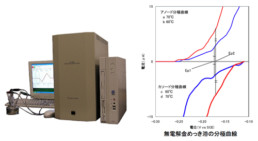
機能めっきのその他のコンテンツ
小型部品用バレルめっき
当社のバレルめっきの特徴
少量ロットから中・大ロット品まで、多彩なサイズ、数量、種類に対応
Cu・鉄・SUS等のプレス、各種セラミック系端子電極に対応
少量からでも短納期対応
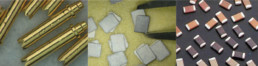
めっき種類 | 鉄系(SUS,コバール等)、 Cu系 | セラミック系部品 (チップ型L/C/R、ヒューズ等) | ||
電解Ni | 光沢 | |||
半光沢 | ||||
無光沢 | 下地めっきとして適用 | |||
無電解Ni | ||||
電解Cu | ||||
電解Sn | 光沢 | |||
半光沢 | ||||
無光沢 | Ni下地 | |||
電解Au | 硬質 | |||
純金 | ||||
無電解Au | 無電解Ni下地、0.03~0.5μ厚 | |||
0.05mm~ L/W=0.5X0.5~10X10mm | セラミック素材、電極種によって 条件出しが必要になります |
機能めっきのその他のコンテンツ
車載用フープめっき
コネクタ用 Snリフローめっき加工
耐ウイスカ―に優れた 端子用めっきとして、1次プレス済のRtoR製品へ連続めっきでのリフロー加工を承ります。リフロー時に形成されますSn-Ni層をコントロールすることで、仕様に応じた硬さの管理を行います。車載用端子製品(プレスフィット、ターミナル端子)向けに量産しています。

Snリフロー前後 めっき層断面観察
リン青銅/Ni下地1.0μm/半光沢Sn1.5μm
リフロー前
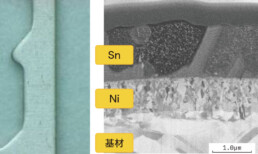
リフロー後
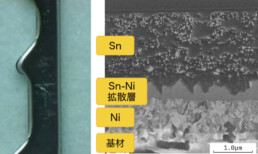
加熱後でもワイアーボンディング強度が安定している連続金めっき
従来の2層(Ni/Au)めっきでは実装時の熱履歴によっては金めっき表面へニッケルが熱拡散することで、酸化膜を形成しワイヤボンディング特性を劣化させていました。
パラジウムめっきを中間層として成膜させると金表面へのニッケル拡散防止には効果があることは確認されていますが、めっき工程が増え、煩雑さやコストアップが懸念されます。
当社は2層(Ni/Au)めっきで加熱後もニッケルが※表面拡散しないワイヤボンディング用金めっきプロセスを開発しました。
材料 | めっき仕様 | 種類 | 板厚 | 幅 | 処理方法 |
各種銅合金 | Ni 1.5μm〜 | 半光沢 | 0.1〜0.6mm | 〜70mm | 全面めっき |
Au 0.20μm〜 | 純度99.9% | 全面/部分 |
機能めっきのその他のコンテンツ
新開発めっき
難素材へのダイレクトめっき加工
簡便に金属皮膜形成が出来ますめっき法にて、従来は適用の難しかった難めっき素材へ直接メタライズを行います。
素材 | 特徴 |
アルミ | アルミ材料は表面に酸化皮膜が形成し易く、めっき皮膜形成のために従来は亜鉛置換を行うジンケート処理を行うのが一般的です。本工程では、ジンケート処理を行わず、直接、めっき処理が可能なため、簡便に金属皮膜形成が可能です。 |
ガラス | ガラスへのめっき皮膜形成は従来、粗化処理によるアンカー効果と触媒付与等のシード層形成が必要でしたが、本工程は特殊な高速DRY工程を組み合わせることで、簡便に、厚付けめっき皮膜形成が可能です。シードレスですのでエッチングも容易です。 |
ポリイミド | DRYプロセスを用いず、めっき皮膜形成が可能です。プライマー塗布方式、直接めっき方式 何れでも対応致します。 |
SUS | Ni下地めっきレスにて、Au,Cuめっきが可能です。 |
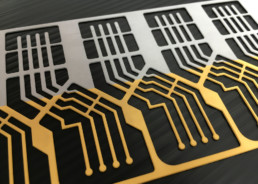
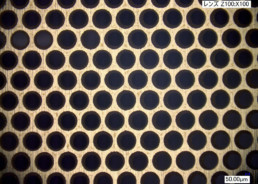
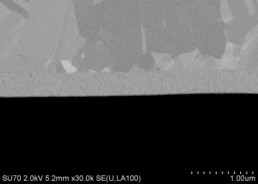
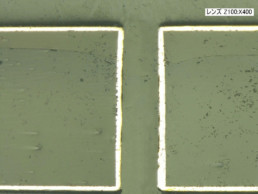
超耐食性Ni めっき加工 A-NI
電子製品等における電極体等におきまして、その接続や集電極においては、長期信頼性面から各種金属電極素材への耐食性向上のための表面処理技術が課題です。
本製品は、0.2μという薄い電解めっき法での塗膜にも関わらず、極めて高い耐食性を有しています。
硝酸ばっき試験
硝酸:69vol% ・温度:室温(23~25℃・時間:1時間、2 時間)
素材:C1020
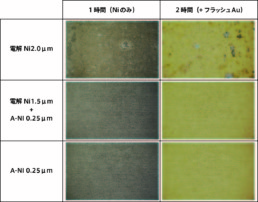
ガラスへのダイレクトめっき
通常、ガラスへの直接めっきは密着性を確保するために、フッ酸等でガラス表面を強力に粗化しますが、弊社開発工程では素材をほとんど荒らさない独自の前処理と、独自の均一性の高い無電解めっきを採用することで鏡面光沢を持っためっき皮膜の形成が可能です。
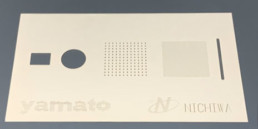
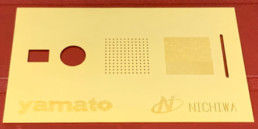
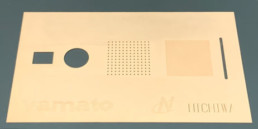
めっき後の外観表面粗さ
素材をほとんど荒らさない弊社前処理により、ナノオーダーの表面粗さで高密着性のめっき皮膜を形成できます。
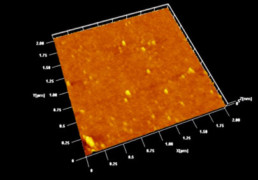
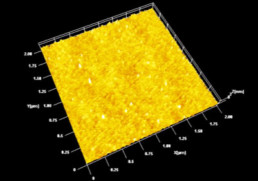
PETフィルムへのCuめっき
通常、PETフィルムへのCuめっきを行う場合、無電解Niめっきをシード層とします。
この場合、CuとNiのエッチングレートが異なりパターンニングが難しいことがあります。
材料グレードは限定的となりますが当社独自のめっき前処理と特殊な無電解Cuめっきにより鏡面を有する密着性の良いCuめっき膜が得られます。
工程
めっき前処理
↓
触媒付与
↓
無電解Cuめっき
↓
電解Cuめっき
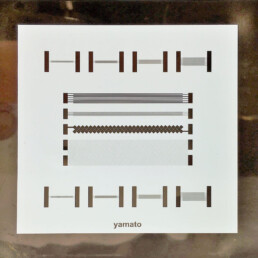
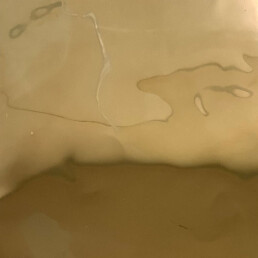
材料 :ルミラーU48(東レ)
材料厚 :0.1mm
銅めっき厚 :10μm狙い(無電解Cuめっき+電解Cuめっき)
有機材料へのめっき加工
各種有機素材へ各種めっき皮膜を均一にコーティングする技術です。
PETメッシュへの無電解Cuめっき
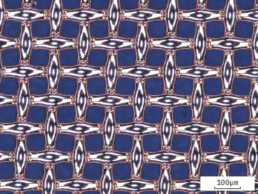
不織布への無電解Cuめっき

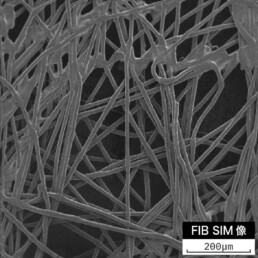
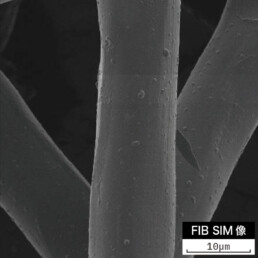
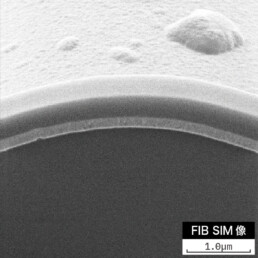
粗化ニッケルめっき
樹脂との密着性向上などの用途に、めっき皮膜を粗化させて表面積を増加させたニッケルめっきが作製可能です。表面全体に凹凸があり、Rzは2.0μmを超えております。
FE-SEM二次電子像(40°傾斜)
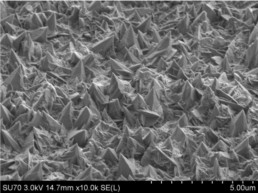
材料:銅板
Niめっき厚:5.0μm〜
凹凸測定(レーザー顕微鏡)
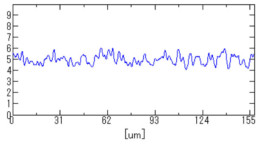
Ra 0.31um
Rz 2.04um
チタン上ダイレクト金めっき、ステンレス上ダイレクト銅めっき
めっき難素材に代表されるチタンにダイレクトで金めっきやニッケルめっきが可能です。素材とめっきの間に欠陥はなく、密着性も良好です。また、ステンレス上にダイレクトに密着の良い銅めっきも可能です。
チタンへのダイレクト金めっき例
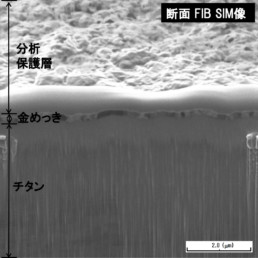
Auめっき厚:0.2μm〜
ステンレスのダイレクト銅めっき例
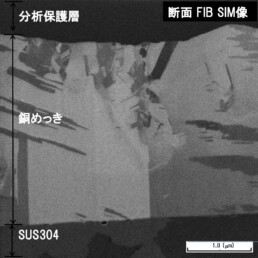
Auめっき厚:3.0μm
不織布へのめっき
不織布線維へ各種めっき皮膜を均一にコーティングする技術です。
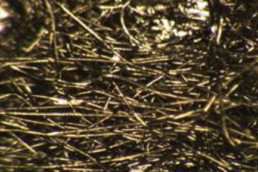
Niめっき厚:0.1μm〜
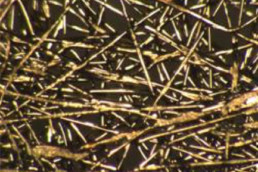
Niめっき厚:0.1μm〜
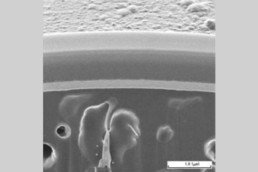
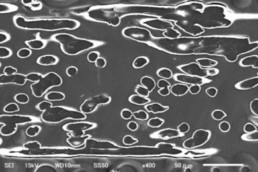
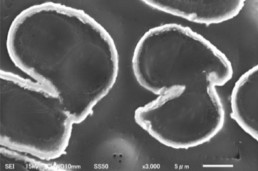
材料:PP織布
Snめっき厚:0.5μm〜
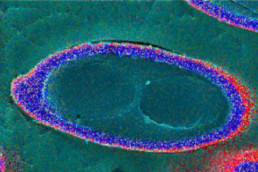
厚Cu基板加工
工数の掛かる厚Cu基板加工について、専用工程にてエッチングから割板、専用検査工程、梱包迄トータルでの加工お手伝い致します。Cu厚は0.1〜2.0mmtまで加工致します。
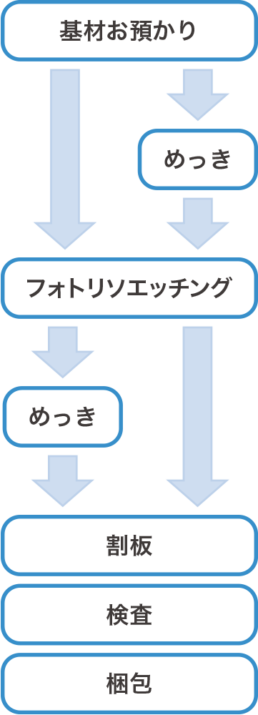
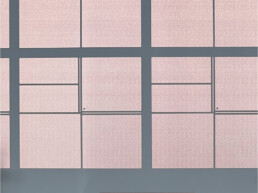
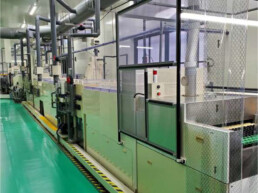
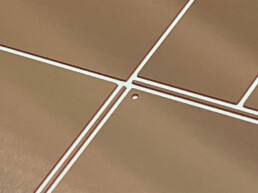
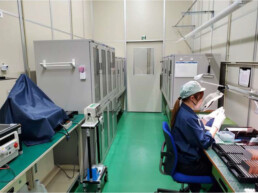
マスク素材(PP, PE布:不織布)へのめっき
当社不織布へのめっき技術を応用して、抗菌作用が有ると言われるAg及びCuをマスク素材であるPP、PE不織布へめっき手法にて皮膜してみました。マスクガーゼのようにマスクに挟んで使用可能です。
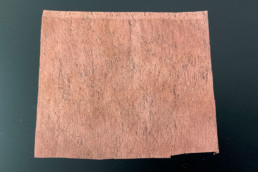
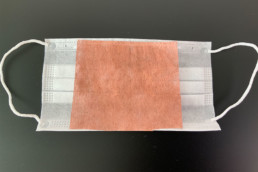
PP布へのCuめっき
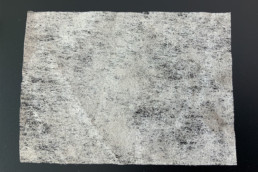
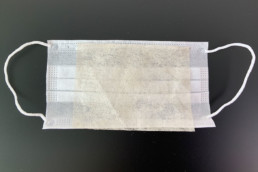
PP布へのAgめっき
機能めっきのその他のコンテンツ
表面解析・測定
所有装置
走査型電子顕微鏡(SEM) エネルギー分散型X線分析装置(EDS) | 日本電子製 JSM-5600(SEM) 日本電子製 JED-2200(EDS) |
フーリエ変換型赤外分光光度計(FT-IR) | VARIAN製 3100-600UMA |
蛍光X線分析装置(※含P率測定) | 日立ハイテクサイエンス製 SEA5120 |
セミオートワイヤーボンディング装置(Auワイヤ) | ウエストボンド製 MODEL 454647E |
セミオートワイヤーボンディング装置(Au、Ag、Cuワイヤー) | TPTジャパン製 HB16 |
ワイヤープルテスター | RHESCA製 PTR-03S |
万能型ボンドテスター | DAGE製 4000Plus |
マイクロスコープ | キーエンス製 VHX-1000 |
密着測定機 | QUAD GROP製 ROMULUS |
高性能集束イオンビーム装置(FIB) | 日立ハイテクサイエンス製 SMI3050 |
電界放射形走査電子顕微鏡(FE-SEM) エネルギー分散型X線分析装置(EDS) | 日立ハイテクノロジーズ製 SU-70 OXFORD製 x-act(EDS [SDD検出器]) |
イオンミリング装置 | 日立ハイテクノロジーズ製 E-3500 |
リフローシミュレーター | マルコム社製 SRS-1C |
レーザー顕微鏡・AFM | Lasertec製 H-1200 |
接触角計 | 協和界面科学製 DM-501 |
自動精密切断機 | 三啓製 アイソメット4000 |
透過X線装置 | DAGE製 XD7600NT |
X線光電子分光装置(XPS) | サーモフィッシャー・サイエンティフィック製 K-Alpha+ |
プラズマ処理装置(プロセスガスO2など) | March製 PCB2800、Max Via |
走査電子顕微鏡システム(FE-SEM+EDX)
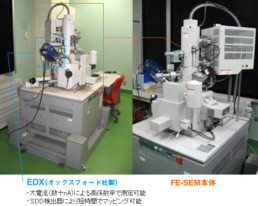
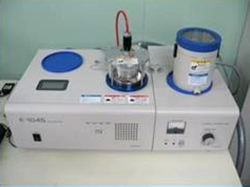
従来SEMとの性能比較
従来SEM | FE-SEM(SU-70) | ||
観察・分析倍率 | ×35~×10,000 | ×35~×300k | |
分解能 | 3~4nm(加速電圧:@15kV) | 1nm(加速電圧:@15kV) |
従来SEMとの画像比較
従来SEM
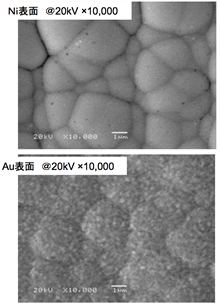
FE-SEM(SU-70)
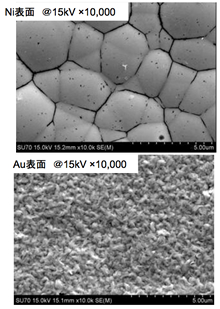
高倍率観察画像(断面)
FIB
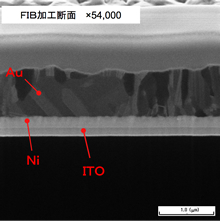
FE-SEM(SU-70)
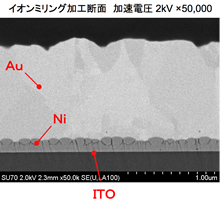
EDX(オックスフォード社製)による分析・・・マッピング
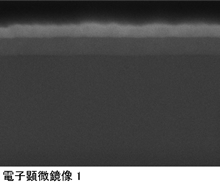
- 分析サンプルNi/Pd/Au、FIB加工断面
- 倍率×30,000
- 加速電圧5kV
- 傾斜60度
- 分析時間3min
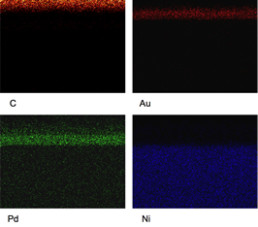
フーリエ変換型赤外分光光度計(FT-IR)
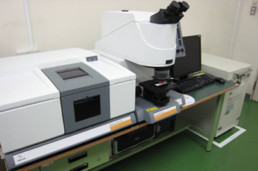
解析記事例
「クリーンルーム内の落下塵(幅20μmの繊維状)の分析」 スペクトルデーターベースの照合結果(赤線)、ポリエステルと判明。 室外からの持ち込み、防塵着からの発塵の可能性が示唆された。
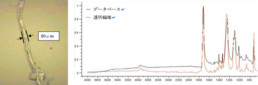
蛍光X線装置
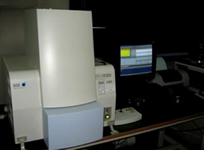
表面元素分析
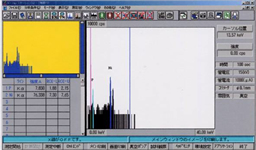
めっき中のPb,Cdの含有量測定など
セミオートワイヤーボンディング装置
ワイヤーボンディング装置
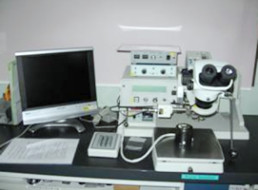
ワイヤープルテスター
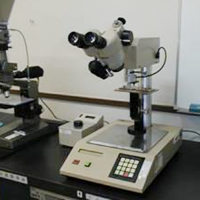
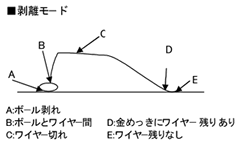
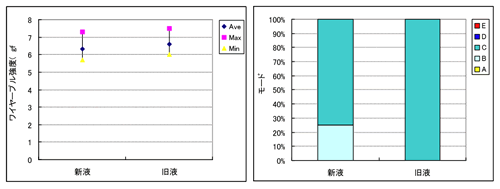
ワイヤーボンダー/ボンドテスター
ワイヤーボンダー(Au/Ag/Cu)
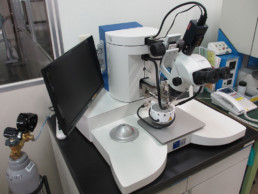
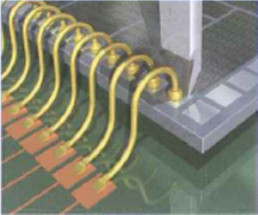
万能型ボンドテスター(プルテスター)
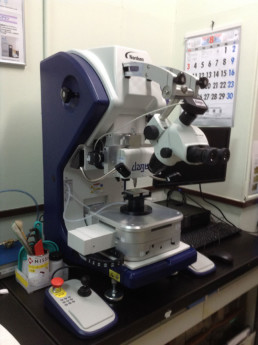
高性能集束イオンビーム装置(FIB)
FIB断面観察
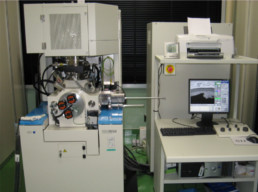
イオンビームによる微細部の加工・観察
最大観察倍率:9万倍
加工限界:幅100μm、深さ50μm
解析事例
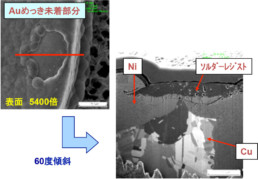
イオンミリング装置
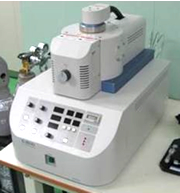
試料にアルゴンイオンビームの一部を照射し、
平坦な試料断面を作製する。
- 最大試料サイズ 20mm×12mm、厚さ5mm
- 使用ガス Ar(アルゴン)ガス
- ミリングレート 100µm/hr (材料:Siの場合)
加工例(PCB-WB端子断面 約3hr加工)
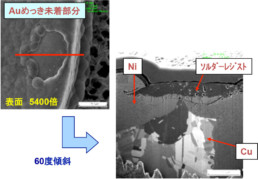
FIB | イオンミリング | |
加工幅 | 数µm~数十µm | 数百µm~1mm |
加工深度 | ~数十µm | ~数百µm |
加工精度 | 数µm単位 | 数十µm単位 |
加工のポイント
- 加工目的位置が、試料端面から100μm以内になるように試料を切り出しておく。
- 試料は端面をヤスリで削るなどして、ある程度平坦にしておく。
- 凹凸が大きいとマスクとの密着が取れなくなるため、上面部をヤスリで削るか又は樹脂で埋め込むなどし、ある程度平坦にしておく。
- ビームによるダメージが大きい場合は、加速電圧・引き出し電圧・スウィングスピードなどの加工条件を調整する。
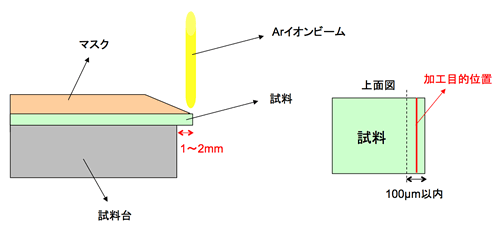
レーザー顕微鏡・AFM
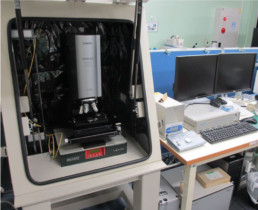
レーザー顕微鏡粗さ測定
測定装置:レーザーテック製 H-1200
レーザー顕微鏡
レーザー光による試料表面観察と表面粗さ測定が可能
測定精度:幅0.1um、高さ0.1um
AFM
試料と探針の原子間力による粗さ測定が可能
測定精度:幅0.01um、高さ0.01um
解析事例

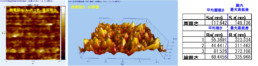
透過X線装置
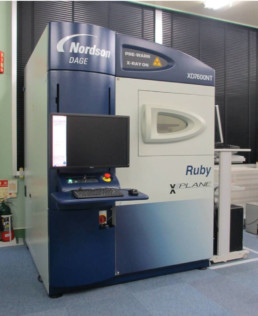
透過X線装置
試料にX線を照射し、透過X線を検出器に投影させ、試料内部を非破壊で観察可能
①2D:上面からの観察
②加熱観察:試料を加熱しながら観察
③CT:観察像を3Dや断層に変換して観察
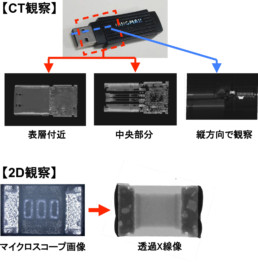
X線光電子分光装置
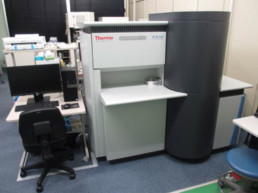
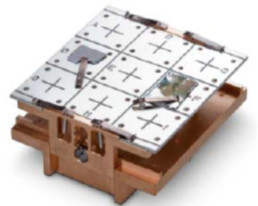
X線光電子分光装置
試料表面にX線(特定波長の軟X線)を照射し、試料から放出される光電子(光電子)のエネルギーを測定することにより、試料表面に存在する元素組成を分析できる装置
対応可能な分析内容
①最表面元素分析
②深さ方向分析(デプスプロファイル)
③絶縁物測定(帯電中和機能)
④状態分析(化学結合状態の分析)
⑤ステージスキャンマッピング分析
装置概要
- X線源:Al
- X線スポット径:30um~400um (※スポット径が大きい方が高感度で、短時間での測定が可能)
- 最大試料サイズ:60mm×60mm
- 最大試料厚み:20mm
- 分析深度:最表面から数nm(~10nm未満)
分析の原理
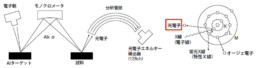
MgやAl表面に電子線を照射すると、長い波長の軟X線が発生。その軟X線を試料表面に照射すると、光電子が放出される。光電子は原子固有のエネルギーを持っているため、そのエネルギーを測定することで試料表面に存在する元素組成や、化学結合状態を分析することができる。(Li~Uまで分析可能)
装置構成
K-Alpha+の特徴
高感度(微量元素も検出可能)
高分解能(ピーク分離がより正確にできる)
全自動により操作性向上
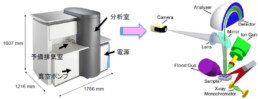
分析事例
①最表面元素分析
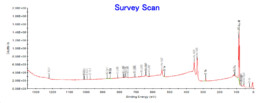
①最表面元素分析
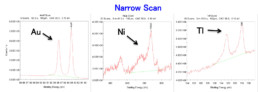
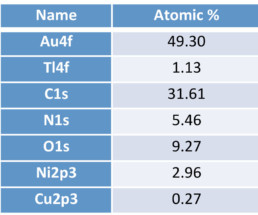
②深さ方向分析(デプスプロファイル)
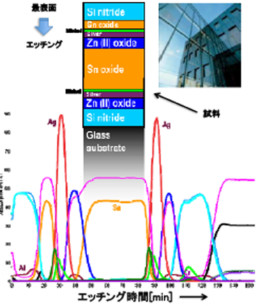
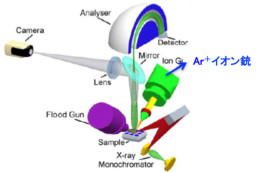
機能めっきのその他のコンテンツ
鉛フリーめっき
半田めっきのウイスカー対策
代替めっきとしてのSnめっき
電子・電気機器における特定有害物質の使用制限として、欧州連合(EU)によるRoHS指令は2003年2月にWEEE指令と共に公布、2006年7月に施行ました。それに伴い、半田めっきにおいては主要成分である鉛が規制されたことから、現状はその多くがSnめっきへ代替されました。ただ、Snめっきにおいてはウイスカという結晶粒子の析出成長による実装後の配線短絡の問題の可能性が指摘されることから、その対策としての皮膜調整が必要となっています。
② ウィスカーを最小限に抑制するためにはめっき工程が非常に重要
ウイスカーの発生そのものをゼロにすることはSnそのものの物性故、一般的には極めて困難であると考えられていますが、皮膜状態や使用環境の管理によって抑制することは可能です。めっき皮膜形成としましては以下の方法が挙げられます。
- 結晶を、大きく、均一な多角形結晶粒子構造にする
- 皮膜中の有機物吸蔵量を少なくする
- 素材に直接めっきせず、バリア層として下地めっきとしてNi層を挟む
- 皮膜層を厚くし、下地との影響を少なくする
- リフローのより 結晶粒子を溶融させ 応力緩和する
当社使用 Snめっきの特徴
析出物中の有機物吸蔵量を低くする
- 添加剤吸蔵量の低減
- 添加剤の副生成物の最小化
析出物結晶サイズを1μmより大きくする
- 効果的な添加剤システム
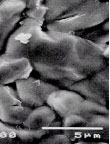
コネクタ用 鉛フリー対応めっき
鉛フリー対応めっき Snリフロー
鉛(Pb)はんだめっきの代替として同等の皮膜特性を有する錫(Sn)めっきを使用する場合、ウイスカー対策が必要です。そのひとつの対策としまして、ウイスカーの発生原因である結晶粒子の内部応力をリフローをかけることで緩和することができます。当社では リフロープロセスを用いたコネクタ用Snリフローめっきを量産しています。
Snリフロー はんだ濡れ性
ゼロクロスタイム (単位:秒)
めっき上がり | PCT:5時間 | PCT:16時間 | ||||
リフロー前 | リフロー後 | リフロー前 | リフロー後 | リフロー前 | リフロー後 | |
1 | 0.33 | 0.80 | 0.47 | 0.70 | 0.58 | 1.08 |
2 | 0.43 | 0.70 | 0.42 | 0.80 | 0.51 | 1.36 |
3 | 0.32 | 0.69 | 0.40 | 0.93 | 0.48 | 1.50 |
4 | 0.32 | 0.71 | 0.50 | 0.95 | 0.30 | 1.04 |
5 | 0.35 | 0.44 | 0.63 | 1.16 | 0.43 | 1.48 |
AVE | 0.35 | 0.67 | 0.48 | 0.91 | 0.46 | 1.29 |
MAX | 0.43 | 1.80 | 0.63 | 1.16 | 0.58 | 1.50 |
MIN | 0.32 | 0.44 | 0.40 | 0.70 | 0.30 | 1.04 |
STD | 0.05 | 0.13 | 0.09 | 0.17 | 0.10 | 0.22 |
測定器:SWET-2000
Sn-3Ag-0.5Cuペースト
ロジン系フラックス
PCT:121℃-100℃RH
機能めっきのその他のコンテンツ
微細コネクタ用フープめっき
当社フープめっき仕様概要一覧
銅系材料
めっき仕様 | めっき厚 | 材厚 | 製品高さ (キャリア含む) | リフロー |
下地Ni 仕上げAu | Ni:0.5~5.0μm Au:0.03~1.0μm | 0.1~1.2mm | MAX 110mm | - |
下地Ni 仕上げSn | Ni:0.5~5.0μm Sn:0.5~8.0μm | 0.1~1.2mm | MAX 110mm | 〇 |
下地Cu 仕上げSn | Cu:0.3~5.0μm Sn:0.5~8.0μm | 0.1~0.64mm | MAX 50mm | 〇 |
下地Ni・Cu(2色) 仕上げAu/Sn | Ni:0.5~5.0μm Cu:0.3~5.0μm Au:0.03~1.0μm Sn:0.5~8.0μm | 0.1~0.64mm | MAX 110mm | 〇 |
下地Ni 仕上げAg | Ni:0.5~5.0μm Ag:0.5~5.0μm | 0.1~0.64mm | MAX 25mm | - |
鉄系材料
めっき仕様 | めっき厚 | 材厚 | 製品高さ(キャリア含む) | リフロー |
下地Ni 仕上げAu | Ni:0.5~5.0μm Au:0.03~1.0μm | 0.1~1.2mm | MAX 110mm | - |
下地Ni 仕上げSn | Ni:0.5~5.0μm Sn:0.5~8.0μm | 0.1~1.2mm | MAX 110mm | 〇 |
SUS材上 ダイレクト Au | ◯ | ◯ | ― | ◯ |
コネクタ金フープめっき 部分めっき
コネクタのフープ材のめっき加工は、プレス工程がめっきの前工程か後工程かで、先めっき加工(条材にめっき)と後めっき加工(プレス材にめっき)の2種類に分けられます。 いずれも素材(銅合金、SUS等) 上に下地のニッケルめっきをして、金めっき等を加工します。 全面めっきも可能ですが、金の単価が高いため、部分めっきという手法で必要な部分的にめっきをします。
コネクタ金フープめっき スポットめっき
スポットめっきについて
スポットめっきとは、必要な部分にだけ金めっきを析出させる技術です。 金の使用量を大幅に削減でき、めっきコストの大幅な低減が可能です。 またムダを省くことで、環境問題の観点からもメリットが得られています。 検査工程において、金めっきエリアを画像処理装置で確認する方法で、全数検査をしています。