CSR
We are committed to the challenge of Clean innovation * What is "Clean Innovation"* Initiatives that our products, technologies, quality, and environment should always be "clean" Together with our customers and partners, we will create technologies to solve social and environmental issues, enhance the value of people's lives around the world, and aim for the future of a sustainable earth and the development of society. We provide all employees who share their management philosophy with opportunities for dialogue, a comfortable work environment, and a place for growth. In addition, we respect diverse cultures and values, take issues seriously, and contribute to the development of the local community. We will promote CSR procurement together with suppliers, taking into consideration the impact of our business activities on society and the environment. We foster an internal culture in which diverse people can maximize their abilities and expertise and make the most of each other' lives. We will also provide opportunities to develop human resources to challenge the transformation of innovative markets to solve global issues. In order to achieve business development through the creation of environmental value with the aim of realizing a sustainable society, we will comply with the requirements applied through our business activities, improve environmental issues, and expand our environmental initiatives with sympathy from people in society. Sustainability refers to the idea of making the world sustainable from three broad perspectives: environment, society, and economy.
It is said that some of the minerals produced in the Democratic Republic of the Congo and the surrounding countries (DRC countries) are the source of funds for armed groups that perform inhumane acts. Among them, the “Financial Regulation Reform Act” (Dodd-Frank Act) was enacted in July 2010, and in Article 1502, columbite-tantalite (tantalum) and tin stone (tin) were used as conflict minerals (conflict minerals). ), gold and iron manganese heavies (tungsten) are listed, and US listed companies are required to disclose the usage status. While international efforts are being made to address the above, the Yamato Denki Group will work to eliminate the use of conflict minerals in order to fulfill its social responsibility as a company in the supply chain.Management Philosophy
"Giving shape to dreams"
in response to our customers' needs.
We will shape dreams, surprises, excitement, and the future.
Everything is loved by the world as a partnerSustainable Policy
1. Products
2. Cooperation with local communities and employees.
3. Supply Chain
4. Human Resource Development and Innovation
5. Environment
Management, Quality and Environmental Targets
1. Reduce complaints and human error with "clean" quality
2. Controlling CO2 emissions by working on SDGs (reducing wasteful raw materials and energy resources, improving work efficiency without waste and unevenness) in a "Kirei" environment
3.Materialize and embody "be kind to people and take good care of others"
Response to conflict minerals
Policy
We do not use conflict minerals that lead to inhumane activities.
If a material procurement investigation reveals that it is a conflict mineral, we will immediately stop trading.
We do not use conflict minerals that lead to inhumane activities. If it is found to be a material that is not limited to conflict minerals and that leads to inhumane activities, we will stop using it immediately.
Machining
Machinig and production equipments
Machining
Small lots for quick delivery of product types and number of machines owned by the many Metal (aluminum, iron, SUS system in general, titanium), and a variety of materials for processing resins5Axis machines , corresponding to the goods polyhedral structure.
Suwa local strengths , cooperation with neighboring manufacturer, supports a variety of processing (laser, sheet metal, printing, heat treatment, polishing, painting, etc.).
Surface manufacturers strengths , corresponding to various surface treatment design and manufacture of parts compatible.
Example: 5axis machining
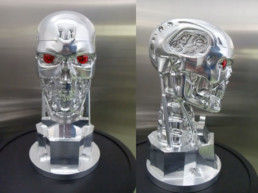
Demonstration ~T2 scalp~
Machine:Mazak Variaxis630 5XⅡ
CAD/CAM: MasterCAM XⅡ
Machining time 18H
Production equipment
Shortening produced by processing in-house sourcing (for short time) can be low cost and when changing the design , in the short term additional machining of fine-tuning during assembly, parts procurement available.
Production Drawing from your concept, improving existing equipment and parts production and assembly drawings to accommodate your various needs flexibly.
Plating for Microelectronics
Plating of electronics substrate and devices for microelectronics
Gold plating for electroless wire bonding for semiconductor wafers
In recent years, while UBM formation (Under Bump Metal) by electroless plating on semiconductor wafer mounting pad electrodes has attracted attention, we have cultivated for many years, utilizing the gold plating technology for printed circuit boards used in SMD, etc., it is possible to process electroless gold plating for stable wire bonding.
Even wafers with a mixture of SR and polyimides can be selectively bonded gold plating on the pad.
Plating Process | Plating Thickness | Wafer Size | Wafer Thickness | Pad | Pad Size |
ENIG (Eletroless Ni/F-Au) | Ni:0.5~10um Pd:0.02~0.8um Au:0.02~0.8um | Small pieces ~8inch *10 inches can be prototyped | 300um~2mm ※300um or less Wafer reinforced by tape as needed | Al | φ10um~ Plating support possible |
ENIGAG (Electroless Ni/Thick-Au) | Al-Si | ||||
ENEPIG (Electroless Ni/Pd/F-Au) | Al-Si-Cu | ||||
ENEPIGAG (Electroless Ni/Pd/Thick Au) | Al-Cu | ||||
Cu |
Micro spot plating for micro connector
Spot plating is plated with technology only where necessary.
Can significantly reduce the amount of use Au.
Reel to reel plating for presses devices for automotive applications
Transport | By vertical transport, both single-tie bar and center carrier are possible. |
Product shape | Materials, primary pressed both possible |
The material amplitude | tandard Max100mmW *Consultation for more cases |
Material thickness | Standard Max0.8mmt *Consultation for no more |
Others | Consultation on mixed specifications of stripe and spot plating, stripe plating (±0.1 mm), etc. |
Four color plating
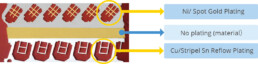
Reflow tin plating with each different thickness
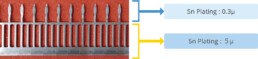
Spot plating
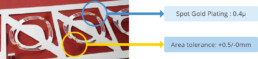
Sn reflow plating for automotive press-fit terminals
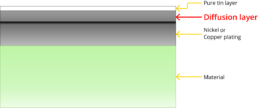
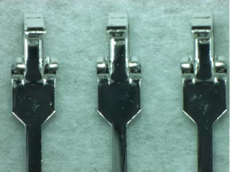
The temperature profile of the reflow is checked by the initial condition setting, and the pure tin thickness and the diffusion layer thickness are controlled. If necessary, we perform cross-sectional observation by CP and IM to ensure the plating layer structure.
Pb free plating
Reflow tin plating
Surface of reflow tin
Zero-cross time (second)
After plating | PCT: 5hrs | PCT: 16hrs | ||||
Before reflow | After reflow | Before reflow | After reflow | Before reflow | After reflow | |
1 | 0.33 | 0.80 | 0.47 | 0.70 | 0.58 | 1.08 |
2 | 0.43 | 0.70 | 0.42 | 0.80 | 0.51 | 1.36 |
3 | 0.32 | 0.69 | 0.40 | 0.93 | 0.48 | 1.50 |
4 | 0.32 | 0.71 | 0.50 | 0.95 | 0.30 | 1.04 |
5 | 0.35 | 0.44 | 0.63 | 1.16 | 0.43 | 1.48 |
AVE. | 0.35 | 0.67 | 0.48 | 0.91 | 0.46 | 1.29 |
MAX. | 0.43 | 1.80 | 0.63 | 1.16 | 0.58 | 1.50 |
Min. | 0.32 | 0.44 | 0.40 | 0.70 | 0.30 | 1.04 |
STD. | 0.05 | 0.13 | 0.09 | 0.17 | 0.10 | 0.22 |
Measurement: SWET-2000 / Sn-3Ag-0.5Cu Solder / Rosin flux
PCT: 121℃-100℃RH
Barrel Plating
Products | A | Chip resistor, Chip capacitor, Chip inductor, Chip filter, SMD products by chip type |
B | Small stamping parts | |
Size | A | min 1.0mm × 0.5mm ~ |
B | Pin: min ø0.5mm × 2mm ~ Plate: min 2.0mm × 1.5mm ~ | |
Plating Thickness | A | Electrolytic Ni, Sn or Au |
B | Electroless Ni, Electro Ni / Electro Au, Electro Ni / Electro Sn, Electro Ni / Electro Ag, Electro Cu |
A) Possible to plate various chip size devices with flexible treatment.
B) Possible to plating small parts with various kind of plating.
Plating on Metal foil
Continuous Ni and Au plating are possible for Cu, stainless steel foil material with the thinnest 10μm thick. (Maximum width 160mm)
It can be used as a reinforcing substrate for battery materials and flexible substrates.
It is possible to form wax materials with gold tin, silver tin, and silver copper by plating method to 30μm thick kovar material.
It is used as a sealing material such as ceramic packages.
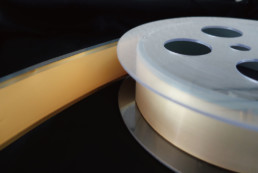
Material Thickness | Plating | Plating Thickness | |
Kovar | 10μm | Au80/Sn20 | 4~20μm |
Ag/Sn5 | ~200μm | ||
Ag/Cu | 4μm~ | ||
SUS・Cu | Ni・Au | 1μm~ | |
Film with Cu | 20μm~ | Ni/Au | 1μm/0.1μm~ |
Gold Tin Alloys by plating forming for Brazing assembly
New technology of plating for microelectronics
Etching free plating without using roughned process
Direct plating of organic film material
Traditionally, when film formation to maintain smooth as glass and plastic, been using dry process is expensive.
Maintaining surface smoothness of the material, can form a solid film by this new plating process.
Maintain the smoothness of nanoscale.
Direct plating on glass
Usually, direct plating to glass strongly roughs the glass surface with hydrofluoric acid, etc., but in our development process, it is possible to form a plating film with mirror gloss by adopting a unique pretreatment that hardly devastates the material and a unique electroless plating with high uniformity.
Zinc-free plating on aluminum
Usually, aluminum materials are highly solubility in acids and alkalis, and it is common to chemically perform zinc substitution (zinc treatment) and perform plating processing.
This technology is capable of plating directly into aluminum materials without zinc replacement treatment.
As a result, the process is shortened, and the partial plating method can be easily performed.
Plating to non-woven fabric
Roughed Ni plating
Nickel plating with an increased surface area by roughing the plating film can be produced for applications such as improving adhesion to resins. The entire surface is uneven and the Rz is over 2.0 μm.
Direct plating for titanium and SUS
Gold plating and nickel plating are possible directly on titanium, which is represented by difficult-to-plating materials. There is no defect between the material and the plating, and the adhesion is good. In addition, copper plating with good direct adhesion on SUS also possible.
Electroless plating on ITO electrade
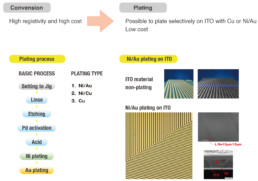
Roughness if surface on ITO and glass substrate after etching
By etching ITO selectively, the surface of glass has not changed while the ITO surface gets four times rough.
Company Overview
Introduction of Yamato
Company Profile
President & CEO
Masahiro Hara
Capital
90million JPY
Established
27/Apl/1944
Employee
410
Product Items
● Plating for micro-electronics devices, substrates and various materials.
● Machining works for tools and metal parts
● Machinery design and manufactureHistory
Apr/1944
Established in
5312 Shimosuwa,Nagano
Jun/1970
Constructed Shimosuwa
Oct/1970
Constructed Matsumoto
Mar/1977
Constructed SUWA
Aug/1983
Constructed Head office building
Aug/1989
Established YamatoTEC
Dec/1996
Registrated ISO9002
Mar/2000
Registrated ISO14001
Dec/2002
Registrated ISO9001#2000
Mar/2005
Constructed R&D building
Mar/2006
Registrated ISO14001#2004
Sep/2008
Established Kohki Div.(Machining and equipment Div.)
Dec/2008
Registrated ISO/TS16949:2000 in Matsumoto
Oct/2012
Established Shinsei (Thailand) Co,.LTD
Nov/2017
Mingrated to IATF16949:2016
Dec/2017
Migrated to ISO2015
ISO9001 :2015/JIS Q 9001:2015
ISO14001 :2015/JIS Q 14001:2015
Jan/2019
Made Shinsei (Thailand) Co.,LTD a wholly owned subsidiary and changed the company name to Yamato Denki (Thailand) Co., LTD.
Jan/2021
Registrated IATF16949: 2016 certification in Suwa-factory
Introduction of Yamato Denki (Thailand)
Company Profile
Location
40/17-19 Moo 5 , Rojana Industrial Park , T.U-Thai, A.U-Thai, Ayuttaya Province 13210
Managing Director
Masayuki Nakayama
Establishment
Construction 28/JUN/2005 Start business on 6 /Dec /2005
Capital
50,000,000 THB (150mil.JPY)(Yamato IND 100%)
Business
Surface treatment For Microelectronics (HDD & CPU & automobile, Camera etc… )
(Electroless Ni Plating / Electro Ni Plating / Electro Au Plating / Chemical Polishing / Ultra clean wash / etc)
Employee
320 persons (Japanese staff 2 persons)as of July 2018
All area
Factory #1 = 5,529㎡ Floor area: 2,250㎡
Factory #2 = 5,550㎡ Floor area: 1,875㎡
Factory #3 = 6,075㎡ Floor area: 2,275㎡
(Including Factory, Waste water treatment area)
Other
ISO9001:2008 ISO140001:2004 ISO/TS16949:2009 Certifired
* TS16949 will be transferred to IATF16949 on November 2018.